Climate change
Endangers health in fundamental ways and the only way we can evolutionary adjust is to bring the farming indoors.

The warming of the planet is gradual, but the effects of extreme weather events – more storms, floods, droughts and heatwaves – are abrupt and acutely felt. Both trends affect some of the most fundamental determinants of health: air, water, food, soil, shelter, and freedom from disease.
The agricultural sector
Is extremely sensitive to climate variability. Rising temperatures and more frequent droughts and floods can compromise food security. Increases in malnutrition are expected to be especially severe in countries where large populations depend on rain-fed subsistence farming.
To be sustainable, agriculture must meet the needs of present and future generations, while ensuring profitability, environmental health, and social and economic equity.
To feed the planet, humanity will need an alternative to traditional farming and the future of farming is indoor.
Vertical farming
Is the practice of growing crops in vertically stacked layers. It often incorporates controlled-environment agriculture, which aims to optimize plant growth, and soilless farming techniques such as hydroponics, aquaponics, and aeroponics. Some common choices of structures to house vertical farming systems include buildings, shipping containers, tunnels, and abandoned mine shafts.
Main Techniques
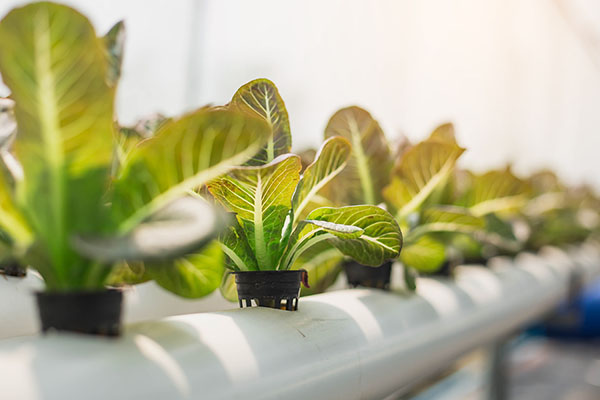
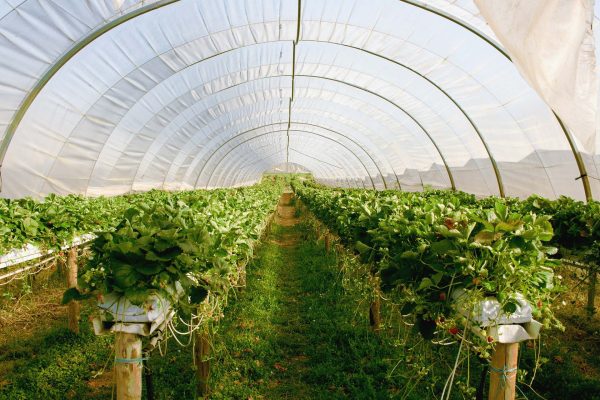
Advantages of indoor farming
- Reliable all-year-round crop production
- Bigger yield per square meter of space
- Better utillisation of space
- Unaffected by adverse weather conditions
- Minimise water usage
- Environmentally friendly
- Savings in fertilizers
- Reduction in chemicals or pesticides
But, there are also high initial investment costs and the whole process relies on technology to ensure the smooth operation of critical systems, such as temperature, lighting, irrigation, and humidity. Vertical farming’s reliance on technology also makes it susceptible to unpredicted events as even the most sophisticated equipment and software can suffer from malfunctions and glitches.
Running a vertical farm is not an easy job as it requires advanced technological and horticultural skills that only a small percentage of people around the world possess. Due to the high tech involved in every stage of the production process, highly educated and trained individuals are needed to set up, run, and maintain a vertical farm.
Here at Hanna Instruments we are dedicated to innovation and have many years of experience in R&D of equipment dedidated to indoor farming and automatization. Hanna Instruments has built a strong reputation for expertise and capability, making this equipment a perfect addition to any vertical farm, grow room, or controlled environment farm.
Fertigation - A key factor in indoor farming
Irrigation is one of the most important operations in agriculture. With proper irrigation the quality and quantity of crops can be significantly enhanced.
Correct irrigation is not a simple process: the quantity of water must be sufficient for crops, and if not, photosynthesis and overall growth is impeded. However, if the amount of water is more than required, plant growth may become excessive, producing a tall, softer and/or damaged product.

Meet our Fertigation System
We design and manufacture a complete, ready-to-install, ferti-irrigation system for our customers.
At first, we collect the information and requests of the agronomist to create a system that corresponds to the actual needs of the customer. Afterward, we analyze the existing infrastructures to be able to interface our systems with the fixture already installed.
Finally, we produce the customized system and proceed with the installation, commissioning, and training of the personnel in charge.
Our ferti-irrigation systems have multiple applications:
- Outdoor farming
- Indoor (soil) farming
- Hydroponics
- Aeroponic
Our fertigation system integrates Hanna Instruments process equipment with high-quality industrial products to create two types of systems:
- Direct injection of nutrients
- Mixing tank
The Advantages of Direct Independent Nutrient Injection
Some fertilizer concentrates (stock solutions) can interact to form insoluble compounds and precipitates. Care must be taken to ensure these concentrates remain separate. Fertilizers containing calcium must not be mixed with fertilizers containing sulfates or phosphates while in concentrated form. The HI10000 utilizes separate and independent nutrient injectors that completely isolate concentrates until they are introduced into the irrigation stream where they are diluted and precisely mixed.
Ca(NO3)2 (Calcium Nitrate) + (NH4)2SO4 (Ammonium Sulfate) > CaSO4 (Precipitate of Calcium Sulfate)
When precipitates form, they tie up key nutrients and make them unavailable to the plants. Precipitates also cause clogging of the irrigation lines and fouling of irrigation equipment.
Fertigation Controller
The Fertigation Controller can control the quantity of irrigation water based on time or volume. Different sectors can be irrigated at different times during the day with different water quantities.
With the Fertigation Controller, each irrigation program provides control of pH and conductivity. When necessary, a specific program performs a pH correction by the introduction of an acid or base into the irrigation water. pH control is based on multiple sensor input and a specific set point, while conductivity control is directly related to the level of fertilization.
When the Fertigation Controller commands the addition of 1 to multiple fertilizers in the irrigation stream, conductivity sensors continually monitor the conductivity of the stream and the overall amount of fertilization is maintained based on a specified set point (limit). The Fertigation Controller can command the addition of multiple (1 to 4) fertilizers to irrigation water. The percentage of each fertilizer is set up by the user and controlled by a specific program based on the conductivity set point.
If a pH or conductivity control problem arises, the program generates an alarm to inform the user. All operations of both control processes are stored in the memory.
The Fertigation controller performs all necessary operations, monitoring, control of irrigation, and fertilization processes. These operations are conducted continuously throughout the day, month and year.
To use and manage the system properly, all the necessary control values must be set (setup mode). During monitoring operations (consulting mode) the user can obtain information about how the system and irrigation process are functioning. Furthermore, the history of all operations for the current and previous days can be accessed.
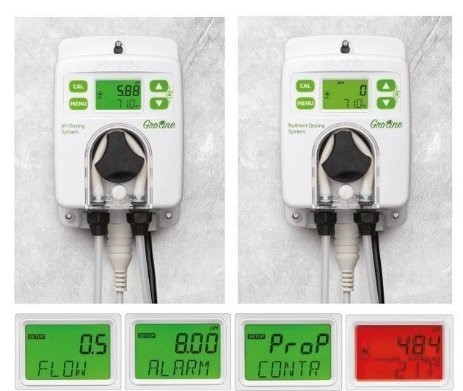
Hanna Instruments is proud to present two new GroLine solutions for the automation of pH and nutrient dosing in cultivation facilities.
HI981413 Nutrient Dosing System
The new HI981413 Nutrient Dosing System is engineered for maintaining the concentration of fertiliser in the nutrient solution used in hydroponics and irrigation water. The meter can be programmed to display results as EC (electrical conductivity) or as TDS (total dissolved solids). The EC results are displayed as mS/cm while TDS is displayed as ppm with a selectable conversion factor from 0.45 to 0.99.
The HI981413 was developed to be an inexpensive solution for the horticulturist to maintain the ideal fertiliser concentrations at all times. Simply insert the probe and injection valve in-line with the recirculation pump and provide the chemical to be dosed.
The HI981413 is available in multiple configurations including a meter and probe option, a kit for in-line mounting, and a complete package that includes bypass loop and panel mounted flow cell. The kit for in-line and flow cell models include aspiration tubing with filter and dispensing tubing with injection valve.
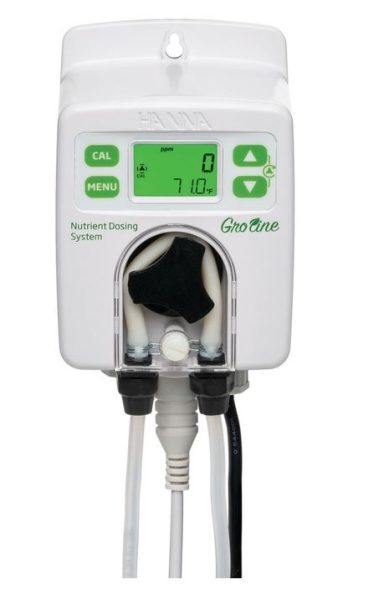
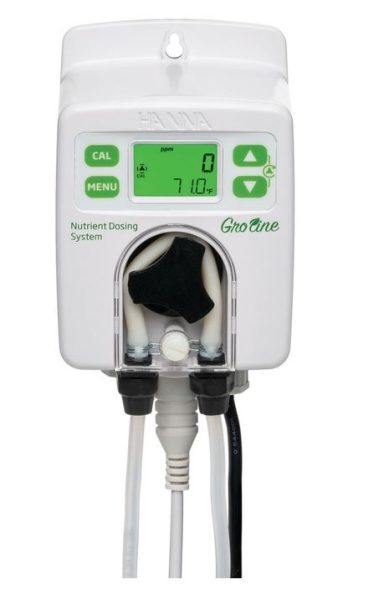
HI981412 pH Dosing System
The new HI981412 is a cost-effective solution for maintaining the ideal pH at all times. Simply insert the probe and injection valve in-line with the recirculation pump and provide the acid to be dosed.
HI981412 is available in multiple configurations including a meter and probe option, a kit for in-line mounting, and a complete package that includes bypass loop and panel mounted flow cell. The kit for in-line and flow cell models include aspiration tubing with filter and dispensing tubing with injection valve.
Author: Nives Vinceković Budor mag.ing.chem.ing.