Boilers are very useful devices in which water (at least in most cases) is heated.
The fluid, its vapors or its heat can then be used for a variety of applications: central heating, sanitation or for boiler-based power generation, just to name a few [1][2].
For industrial applications, a boiler tends to be permanently under pressure and possesses a high throughput of water.
It thus needs to be kept in good condition to withstand these strains.
1. Maintenance of Boiler Functionality
Boiler efficiency depends on a lot of factors:
- how well it retains heat?
- how fast the heat is transferred to the water?
- how much of the transferred heat is not lost to side reactions?
and much more…
These factors very much depend on the contents of the boiler feed water, as well as the materials the boilers and the lines are made of.
Ensuring that these components are in an optimal state for their uses is crucial not only to keep efficiency up, but also to avoid accidents due to deteriorate lines or heat spots.
2. Water treatment
Treating regular water before transferring it to the boiler system is key to a long boiler lifespan and efficacy, as there exist a multitude of ions and molecules which cause side reactions which are harmful to the system.
There are multiple ways to perform water treatment:
⇛ Reverse Osmosis
⇛ Deareation
⇛ Oxygen scavengers
The most important part of water treatment is reverse osmosis.
This process purifies water by applying a pressure which is greater than the osmotic pressure. This pressure pushes the liquid through a partially permeable membrane, which holds back greater particles, molecules and ions.
As a result, the water that has been pushed through the membrane possesses a high purity.
This results in the prevention of several problems such as:
- Foaming (impurities)
- Scale Formation (carbonates)
Scale formation is a specific kind of fouling, which is the deposition of solids on surfaces.
In the case of scaling, these are mostly minerals and/or salts that precipitate in the boiler tube or on heat transfer surfaces.
This results in a slower heat transfer and in turn, creates local spots which are prone to overheating, and can end up rupturing the boiler tube.
There are many approaches how to minimize oxygen and carbon dioxide, which end up harming the boiler system causing Corrosion and Scaling from Iron.
It is thus vital that the feed water of the boiler contains a very low concentration of these molecules.
This is usually achieved by deaeration, which can be done using one of many approaches, for example vacuum deaerators, mechanical pumps or deaeration heaters.
Reducing and monitoring the oxygen content is thus key for the longevity of the boiler system.
3. Water Monitoring
While implementing devices and chemical methods to reduce or circumvent negative impacts is necessary, without control, it is difficult to tell how much impact each of the taken measures has.
Additionally, monitoring certain parameters can give a lot of clues about the status of the system and act as a warning system.
As more and more data is gathered, monitoring helps to find the optimal range of parameters.
This ultimately raises the boiler efficiency and potentially reduces the amount of chemicals that have to be used, thus saving costs in the long run.

HI510 • HI520
Single and Dual-Channel Universal Process Controllers
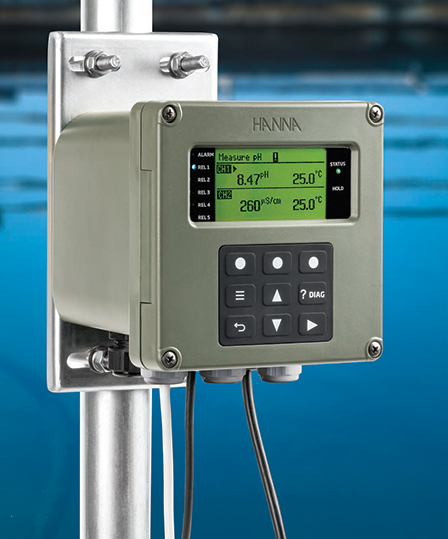
HI510 and HI520 are advanced process controllers that can be configured for applications requiring monitoring and/or control of four main water-analysis parameters:
- pH
- Conductivity
- Dissolved Oxygen
- ORP
These controllers feature a digital probe input(s) that automatically detects and updates the controller with the parameter that it measures.
pH monitoring
One of the most important parameters to monitor is the pH value.
This is due to its influence on many different processes:
- speed of oxygen scavenging
- at a high pH value, foaming and scaling tends to occur
- at a low pH, corrosion tends to occur
- silicate deposition
- Caustic embrittlement
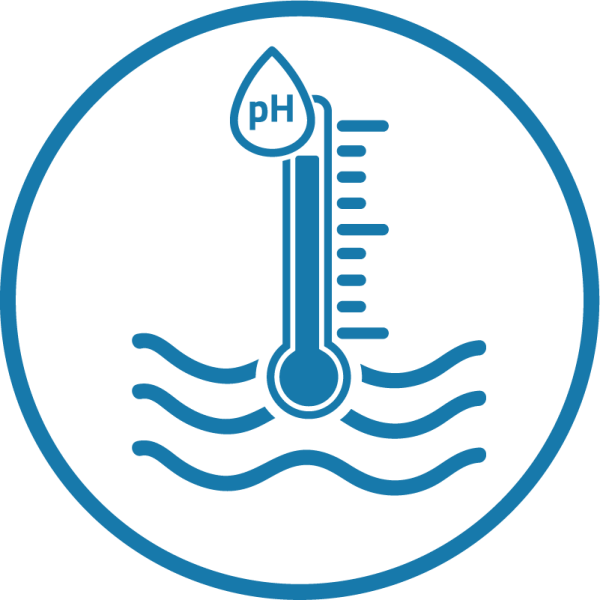
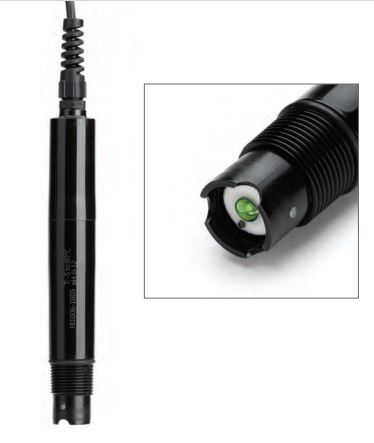
For monitoring, a built-industrial pH electrode, such as the HI1006-38 series, is recommended due to its durability and resistance to heat.
While a common recommendation is to keep the pH at 8.5 (by using NaOH, for example), it is important to note that the optimal pH depends on the alloy used in the boiler and the chemical treatment of the water, among other factors.
ORP monitoring
The Oxidation-Reduction Potential is a great indication for the content of free chlorine.
It is thus the parameter of choice in the sanitation/desinfection section of the boiler system and can be monitored with the HI2004-18 series

Conductivity monitoring
Constantly monitoring the conductivity of the feed water can give insight about its content of charges species, and acts as warning against foaming, as well as corrosion.

This can be done using process electrodes, such as the HI7630-28
Dissolved Oxygen monitoring
As previously mentioned, the removal of oxygen is important to ensure a long lifespan of the boiler.
Monitoring the oxygen content with respect to the oxygen scavengers used does not only ensure that the O₂-concentration will not be too high, it will also allow the user to find the sweet spot for the scavenger concentration, thus avoiding unnecessary expenses.
One such monitoring device would be the HI7640-58 series.
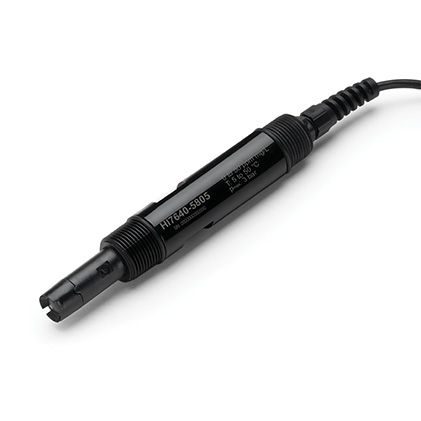
4. Water Analysis
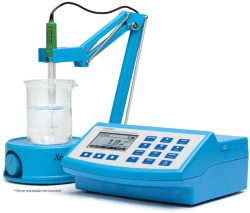
While continuous monitoring is important, it is impossible to monitor all parameters in each section of the boiler system.
Thus, regular sampling and water from these sections is key to truly understand the status of the system.
pH analysis
HI99141
pH Meter for Boilers and Cooling Towers
The specialized HI729113 electrode features a titanium body, flat tip, and porous PTFE junction making it perfect for the pH measurement of treated boiler, feed water, and steam condensate.
Conductivity (EC) analysis
HI98197
Ultra Pure Water
EC/Resistivity Meter
The HI98197 is supplied complete with all accessories necessary to perform high purity water measurements packaged into a durable carrying case.
The accessories include a stainless steel flow cell and a threaded four ring conductivity probe that allows for high resolution 0.001 μS/cm for conductivity and 0.1 MΩ * cm for resistivity readings.
- Stainless steel flow cell
- Four ring conductivity/resistivity probe
- 0.001 μS/cm resolution
Dissolved Oxygen analysis
HI98198
Optical Dissolved Oxygen Meter
Perfect for the field or for the laboratory, the Quick Connect probe requires no membranes, no filling solution and no warm-up time so you can measure without hesitation.
Your meter comes complete in a rugged, custom carrying case for easy transportation.
- Optical DO technology for fast and stable readings, even in tough environments.
- Digital probe with Smart Cap Technology eliminates costly, tiresome membranes and solutions.
- An IP67-rated waterproof, rugged body makes this portable meter ideal for field use.
Complete water analysis can be done using a multiparameter photometer (HI83300, HI83305) or spectrophotometer (HI801).
Oxygen Scavengers analysis
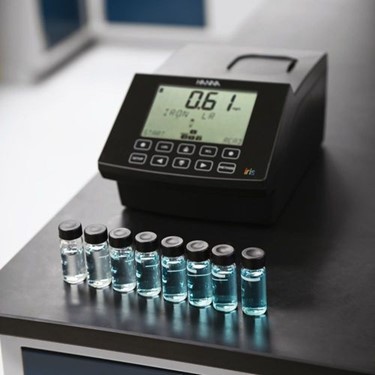
While mechanical/physical deaerators do the most of the work, these are usually combined with chemical oxygen scavengers.
These substances bind oxygen, which dropping its concentration to an even lower level [6].
In boiler systems, the most commonly used oxygen scavengers are sodium sulfite, sodium bisulfite, hydrazine and their catalysed versions. It is also possible to use organic compounds, like hydroquinone and ascorbate.
Hydrazine is, due to it’s toxic properties, expected to become more limited in the foreseeable future.
Carbonates analysis
Carbonates form scales which are typically granular and porous.
The most common deposit is limescale, which mainly consists of calcium carbonate (CaCO3, reaction (2)) and is fairly difficult to clean [4]. This substance forms in the presence of calcium/magnesium and bicarbonate (HCO3-), whereas the latter can stem directly from dissolved carbonates (CO32-, reaction (1)), or from carbon dioxide (CO2, reaction 1):

If the water is hot or the pressure is low enough, the release of gases is thermodynamically preferred, and thus the equilibrium of reaction (2) moves to the right.
Since avoiding heat is not an option for boiler systems, it is of utmost important that both the content of carbonates and carbon dioxide is as low as possible. In the case of carbon dioxide, this can be achieved via de-aeration and degassing.
Measurements can be made in several ways:
Water hardness / Ca – hardness / Mg-hardness
Sulfates analysis
Unlike carbonates, sulfates are usually dense, hard and brittle.
Calcium sulfate is the most common example for scaling, has a low solubility, and it forms according to reaction (3)[5]:

When calcium sulfate dissolves in water (revers reaction of (3)), it releases energy in the form of heat.
Cooling the water increases the solubility of this salt, as the release of thermal energy to colder substances is favored. Conversely, higher temperatures decrease the solubility of calcium sulfate, and cause precipitation. Therefore, the deposition of carbonates and calcium sulfate is more prevalent on hot surfaces, although for different reasons.
Alkalinity analysis
High alkalinity stemming from carbonates is quite problematic for steam generating boilers.
The carbonates will react to CO2, a gaseous component, which will be transferred with the steam.
Once it reaches a cool, wet surface, it forms carbonic acid (H2CO3, see reaction (5)), which can corrode the steam lines.
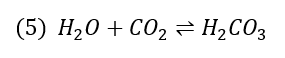
Aside from using pure water, an additional method to solve these issues would be to utilize polyphosphates as dispersants.
In their presence, calcium reacts and precipitates as tricalcium phosphate, which is insoluble in water.
Therefore, it can be disposed of via the bottom of the boiler or blowdowns.
Free Chlorine analysis
As water cannot be contaminated by microorganisms, such as bacteria, viruses and algae, it is important to sterilize the system to prevent their growth.
These microorganisms would otherwise create films on the boiler and line surfaces, which can cause blockage or corrosion.
Adding chlorine to the water produces ClO– and HClO–; together, they are denoted as “free chlorine”.
HClO, the active compound of the two, is very effective at killing the aforementioned microorganisms, thus preventing the problems their growth would cause.
It is recommended to keep the level of free chlorine at 0.05 to 0.1 mg/L, as values below this region do not guarantee the killing of the contaminants.
Silica analysis
Silicate deposits are usually very hard and dense, even more so than sulfates.
Similar to the iron oxides, they consist of silicon and oxygen and they too, are a substance class with different compositions. But unlike the previous examples, the precipitation problem of silicates is not just limited to the boiler surfaces.
Silica can transfer into the gas phase, until an equilibrium with the liquid phase is reached. This equilibrium is influenced by pressure, temperature and the pH value [7].
In general, the higher the pressure and temperature and the lower the pH value, the higher the silicate content in steam. This means that silicates can be carried over via steam and precipitate on cooler surfaces, such as steam turbines.
Silicates are chemically inert, meaning they barely react with chemicals. This makes them very challenging to remove. Thus, preventive and corrective measures are a must and they generally tend to be cheaper than removing the scales or replacing the affected parts.
One such corrective measure would be an increased boiler blowdown to decrease the silica content.
This grants the operator time to find the reason for the silica contamination and fix it.
Providing the right setup for the boiler system and maintaining a good praxis of constant monitoring and regular analysis, will make sure that your boiler will function at its best for a long time.
Have questions?
Contact a Hanna Technical Specialist at [email protected] or using our contact form.
SOURCES:
[1] Steingress, Frederick M. (2001), Low Pressure Boilers (4th ed.), American Technical Publishers
[2] Steingress, Frederick M.; Frost, Harold J.; Walker, Darryl R. (2003), High Pressure Boilers (3rd ed.), American Technical Publishers
[3] Anthony A. Miele (1945); Boiler Tube Performance (PDF). Ohio State University
[4] Hermann Weingärtner (2006, December), “Water” in Ullmann’s Encyclopedia of Industrial Chemistry, Wiley-VCH, Weinheim
[5] Franz Wirsching (2012), “Calcium Sulfate” in Ullmann’s Encyclopedia of Industrial Chemistry, Wiley-VCH, Weinheim
[6] Sendelbach M. (1988), Boiler-water treatment: Why, what and how. Chemical Engineering, 95(11), p. 129
[7] A. Bahadori, H.B. Vutharulu (2010), “Prediction of silica carry-over and solubility in steam of boilers using simple correlation”, Applied Thermal Engineering, Vol. 30, pp. 250-253
[8] Krishnamurthy et al. (1 August 2007), Engineering Chemistry, PHI Learning Pvt. Ltd. p. 146
[9] Mellor J. W. (1941), Intermediate Inorganic Chemistry, London: Longman, Green & Co. p. 202
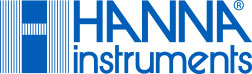